
Our Process
- Home
- Page
Our Manufacturing Process
Step 1 : Draw Design
Jewellery designers create the design on paper. The directors study the designs. Applying market patterns and their foresight, they change the designs suitably. These designs are circulated to their clients, who select the ones they wish to order. Wax pieces are made as per model.
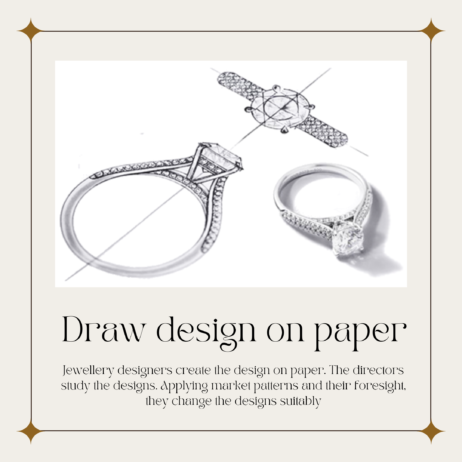
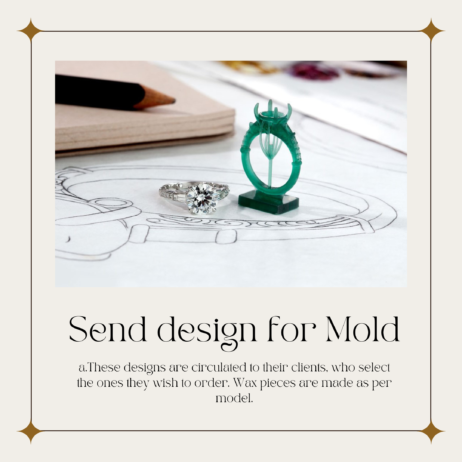
Step 2 : Design Mold
After the design is finalized, the next jewelry manufacturing process is to create wax model with all the fine details by a computer-aided wax-making machine. The computer file of the 3D model is transferred to a milling machine to cut out a wax model or a 3D printer will grow an exact replica of the jewelry. The end result of wax model can be mathematically precise and offer mechanical feel to it.
Step 2 : Design Mold
After the design is finalized, the next jewelry manufacturing process is to create wax model with all the fine details by a computer-aided wax-making machine. The computer file of the 3D model is transferred to a milling machine to cut out a wax model or a 3D printer will grow an exact replica of the jewelry. The end result of wax model can be mathematically precise and offer mechanical feel to it.
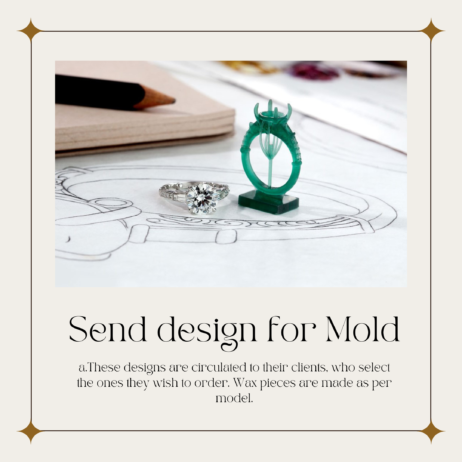
Step 3: Vulcanization
The fine carved wax is then imbedded in a metal cylinder which will be filled with plaster-like investment and left to harden. The mold containing the hardened plaster is heated in an oven at extreme temperatures to burn away any wax traces, leaving a hollow impression of a jewelry shaped in the hardened investment. The selected designs are then vulcanized, Rubber dies are prepared and Ready for moulding
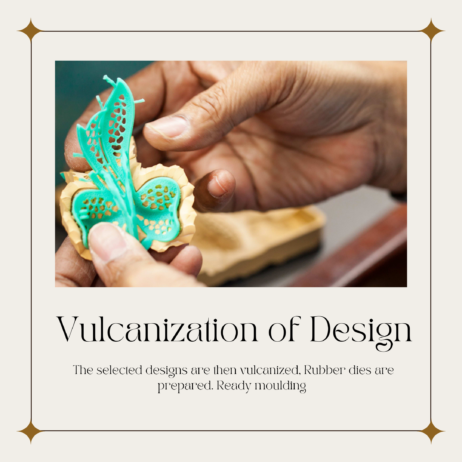
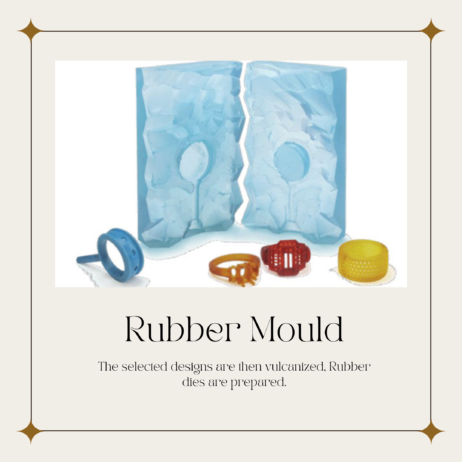
Step 4 : Rubber Mould
The silver master model is then packed into a fat sandwich of special mold rubber and squeezed tight under high heat and pressure until it forms a solid block. The rubber forms itself around the master model, creating a perfect three-dimensional impression of the piece of jewelry. The rubber is cut in half to remove the silver master. Then the rubber is put back together and the final result is the rubber mold which can be accurately duplicated for thousands of wax replicas for mass production.
Step 4 : Rubber Mould
The silver master model is then packed into a fat sandwich of special mold rubber and squeezed tight under high heat and pressure until it forms a solid block. The rubber forms itself around the master model, creating a perfect three-dimensional impression of the piece of jewelry. The rubber is cut in half to remove the silver master. Then the rubber is put back together and the final result is the rubber mold which can be accurately duplicated for thousands of wax replicas for mass production.
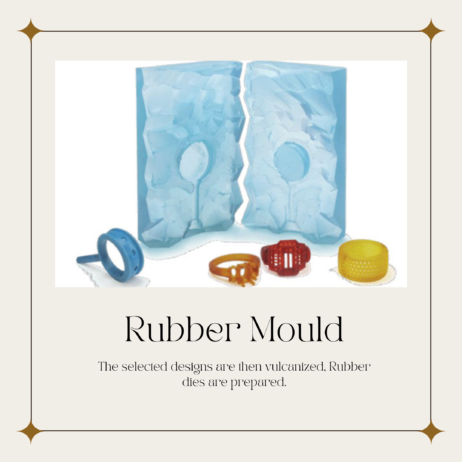
Step 5 : Artificial Model
The best part of the rubber mould is that the designs remain safe, well protected and embedded within it and thus can be used to create replicas of the jewellery design in the future. The tricky thing is that during the jewelry manufacturing process of turning this model into a final piece, the scale will shrink slightly, depending on the materials used. So the model maker needs to make sure that the original wax model is slightly larger than desired
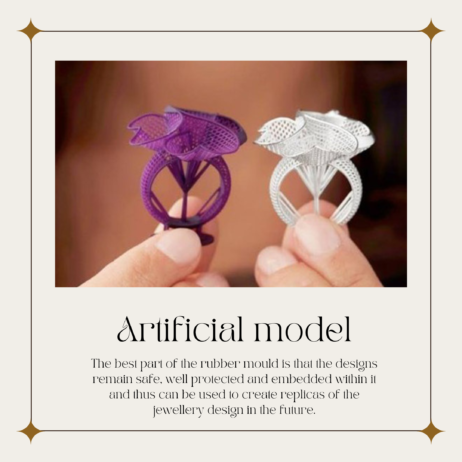
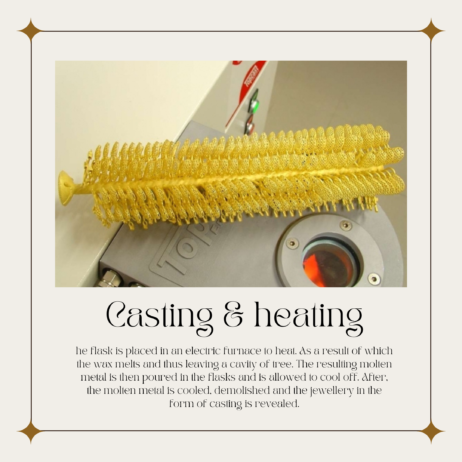
Step 6: Wax Tree
The wax pieces are produced from rubber moulds made of silver master. The process of waxing involves placing the rubber mould on the commercial wax injector machine and then pressure injected into the cavlry in order to create wax models. these wax models are being used for casting.
Step 6: Wax Tree
The wax pieces are produced from rubber moulds made of silver master. The process of waxing involves placing the rubber mould on the commercial wax injector machine and then pressure injected into the cavlry in order to create wax models. these wax models are being used for casting.
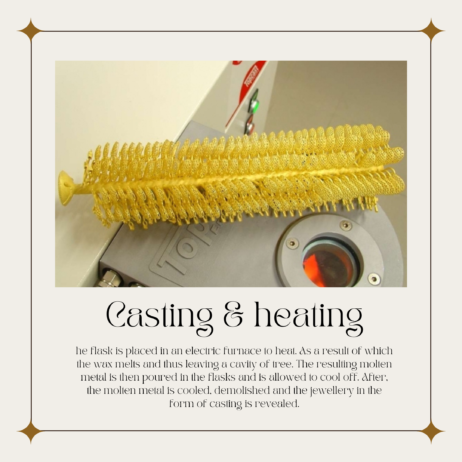
Step 7: Casting & Heating
The flask is placed in an electric furnace to heat. As a result of which the wax melts and thus leaving a cavlry a tree. The resulting molten metal is then poured in the flasks and is allowed to cool off. After, the molten metal is cooled, demolished and the jewellery in the form of casting is revealed.
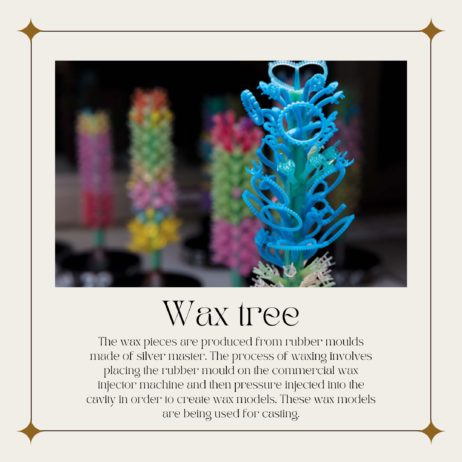
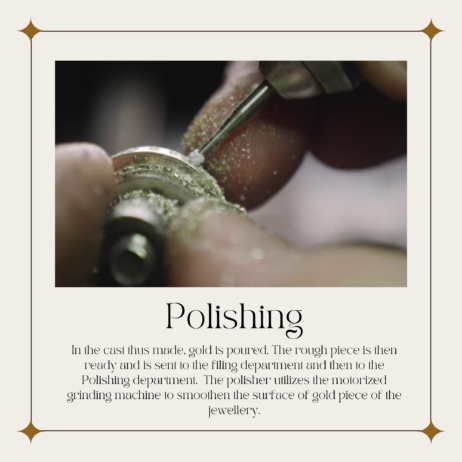
Step 8: Polishing
In the cast thus made, gold is poured. The rough piece is then ready and is sent to the filling department and then to Polishing department. The polisher utilizes the motorized grinding machine to smoothen the surface of gold piece of the jewellery.
Step 8: Polishing
In the cast thus made, gold is poured. The rough piece is then ready and is sent to the filling department and then to Polishing department. The polisher utilizes the motorized grinding machine to smoothen the surface of gold piece of the jewellery.
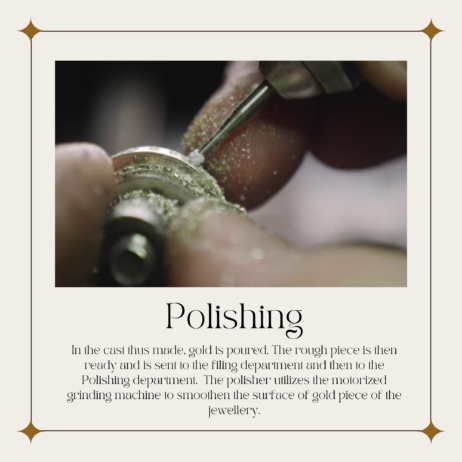
Step 9: Stone Selling
Stone settling is one of the essential stages of jewelry manufacturing, in which gemstones are attached in a metal casting. The pleasure and challenge of including gems in a jewelry object, apart from the intrinsic beauty of the gem.
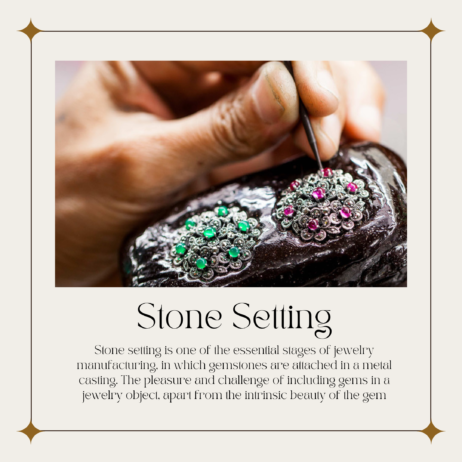
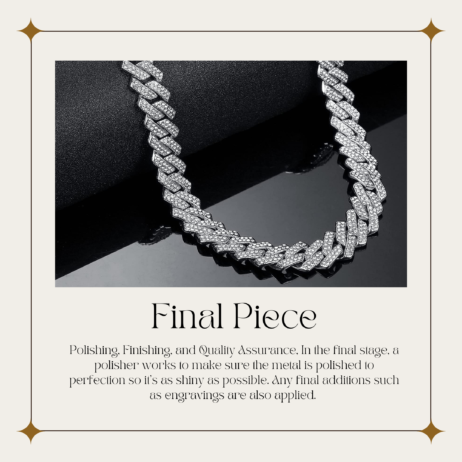
Final Destination
Polishing, Finishing, and Quality Assurance. In the final stage, a polisher works to make sure the metal is polished to perfection so it’s as shiny as possible. Any final additions such as engravings are also applied.
Final Destination
Polishing, Finishing, and Quality Assurance. In the final stage, a polisher works to make sure the metal is polished to perfection so it’s as shiny as possible. Any final additions such as engravings are also applied.
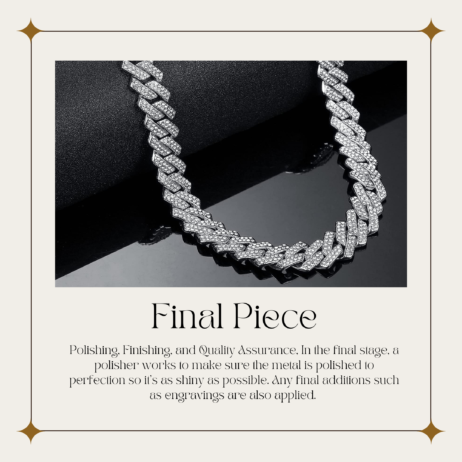